When it comes to reducing construction and demolition waste directly on-site, few tools offer the versatility, efficiency, and robustness of the MB Crusher Bucket. Designed to be mounted on excavators, these attachments transform hydraulic power into mechanical crushing force, allowing operators to repurpose materials without leaving the worksite. In this article, we explore everything a prospective buyer needs to know about MB Crusher Bucketsβfrom functionality and compatibility to safety, maintenance, and technical specs.
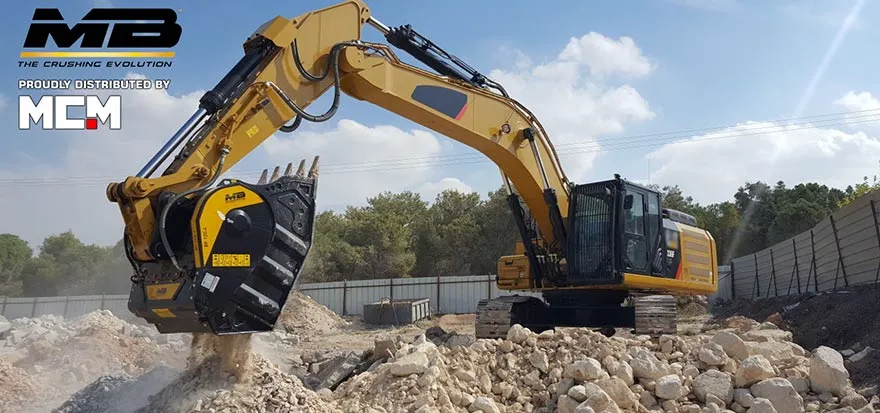
What Is an MB Crusher Bucket?
An MB Crusher Bucket is a high-performance attachment designed to crush and reduce inert materials such as concrete, bricks, rock, and demolition debris into reusable aggregates. These buckets are mounted on excavators and utilize the host machineβs hydraulic system to power robust crushing jaws.
Available models include:
Each model is tailored to different excavator sizes and operational needs.
Key Benefits
- On-Site Recycling
Crush materials directly on-site, reducing transportation costs and environmental impact. - Wide Compatibility
Can be mounted on excavators from 5 tons up to 43 tons, depending on the model. - Hydraulic Precision
Engineered to operate efficiently within the hydraulic parameters of standard excavators. - Customizable Output
Adjustable jaw openings allow for customizable material sizesβfrom 15mm to 150mm, depending on the model.
Compatibility and Hydraulic Requirements
Before purchasing, itβs essential to ensure that your excavator meets the hydraulic flow and pressure requirements for your chosen bucket model. For instance:
- The BF60.1 S4 requires 120β150 L/min flow and 230β280 bar pressure.
- The largest model, BF135.8, needs up to 360 L/min flow.
Intended Use and Limitations
The MB Crusher Bucket is built for crushing inert demolition materials, such as:
- Concrete
- Bricks
- Rock
- Porphyry and granite (with size limitations)
However, it is not intended for:
- Flammable or explosive materials
- Submerged operation
- Lifting or transporting materials
- Use in extreme temperature conditions (below -20Β°C or above 100Β°C).
Operation and Safety
Safety is paramount. Key safety features include:
- Adhesive warning labels on critical areas (e.g., crushing zones)
- Emergency shut-off protocols
- Personal protective equipment (PPE) requirements: gloves, helmet, boots, eyewear, and ear protection.
To unblock jammed material, the unit should be tilted vertically with the blade facing downwards. Never attempt to manually remove jammed materials.
Maintenance Essentials
Routine maintenance ensures performance and longevity:
- Greasing: Every 10 hours during the first 100 hours, then every 30 hours.
- Belt Tension & Flywheel Check: Every 160 hours.
- Jaw and Toggle Board Inspection: Every 500β1000 hours depending on usage.
A comprehensive maintenance checklist is provided in the manual and should be followed strictly.
Performance and Adjustments
The buckets feature adjustable jaws and a fine-tunable hydraulic rotation speed:
- Jaw distance can be modified using shims to control output size.
- Rotation speed varies per model and can be adjusted via a handwheel in the hydraulic control unit.
Built to Last
Constructed with high-resistance steel and replaceable wear parts (jaws, toggle board, belts), MB Crusher Buckets are designed to withstand heavy-duty applications. Exploded views and parts listings are available in the manual to simplify repairs and replacements.
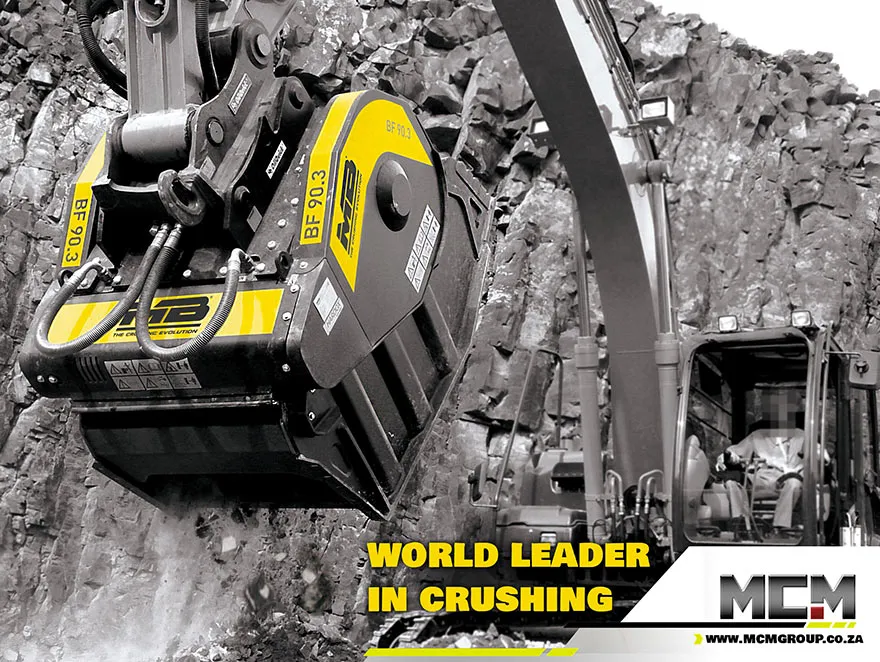
Conclusion: Is an MB Crusher Bucket Right for You?
If your operations involve frequent demolition or material repurposing, the MB Crusher Bucket offers a powerful, efficient, and environmentally responsible solution. With various models to match different excavator sizes and job requirements, and backed by MBβs global support network with MCM’s hands-on support, itβs an investment that pays for itself in mobility, productivity, and versatility.
For more information, contact MB at info@mbcrusher.com or visit their website www.mbcrusher.com.